The Advancements and Importance of Pressure Die Casting Products
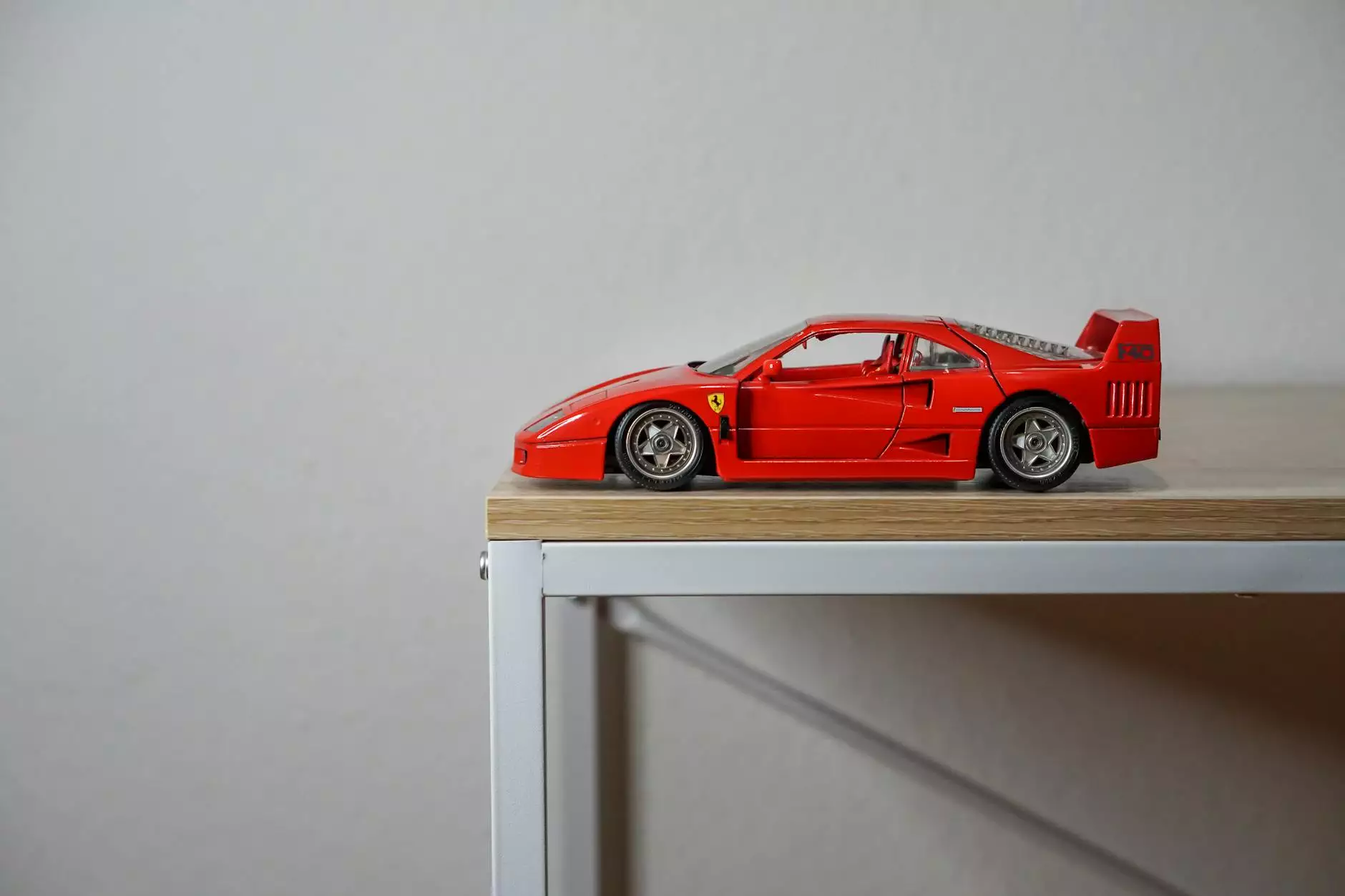
In today's rapidly evolving industrial landscape, pressure die casting products have emerged as a cornerstone in manufacturing, particularly for industries requiring high-performance, durable components. This technique, which allows for the mass production of complex metal parts, stands out for its myriad benefits. At deepmould.net, we specialize in providing high-quality solutions in metal fabrication, including a comprehensive range of pressure die casting products that meet various industrial standards.
Understanding Pressure Die Casting
Pressure die casting refers to the process of injecting molten metal into a mold at high pressure. This technique is celebrated for its ability to create complex shapes with excellent dimensional accuracy and a superior surface finish. Unlike traditional casting methods, pressure die casting ensures that the metal fills the mold cavity completely, leading to stronger and more reliable products.
How Does Pressure Die Casting Work?
The process of pressure die casting involves several critical steps:
- Preparation of the Die: The die, typically made of hardened steel, is meticulously designed and manufactured to achieve the desired component shape.
- Melting the Metal: The metal, usually aluminum or zinc-based alloys, is heated to its melting point to form molten metal.
- Injection of Molten Metal: Using a high-pressure system, the molten metal is injected into the die, filling it under extreme pressure.
- Cooling and Solidification: Once filled, the metal cools and solidifies, taking the shape of the die.
- Die Opening and Part Ejection: After cooling, the die is opened, and the finished part is ejected, ready for further processing or use.
Benefits of Pressure Die Casting Products
The popularity of pressure die casting products can be attributed to several key advantages they offer:
- Efficiency: The ability to produce large volumes of consistent parts quickly makes pressure die casting an efficient choice for manufacturers.
- High Complexity: This method can create intricate shapes that would be difficult or impossible to achieve with other casting methods.
- Excellent Surface Finish: Parts produced through pressure die casting have a smooth surface finish that often requires little to no post-processing.
- Cost-Effectiveness: Due to the reduction in material waste and labor costs, pressure die casting can be a more economical choice in large production runs.
- Strength and Durability: The process produces components with superior mechanical properties, making them suitable for demanding applications.
Applications of Pressure Die Casting
Pressure die casting products play an integral role across a multitude of industries. Below are some prominent applications:
1. Automotive Industry
The automotive sector is a significant consumer of pressure die casting products. Components such as engine blocks, transmission housings, and various brackets are commonly manufactured using this method due to their lightweight and robust characteristics.
2. Aerospace Industry
Aerospace applications require components that not only meet strict safety standards but are also lightweight. Pressure die casting allows manufacturers to produce complex parts such as casing and structural components that are critical in aircraft design.
3. Electronics Industry
In the electronics field, pressure die casting is used to manufacture housings and enclosures for various devices, ensuring protection and durability while maintaining aesthetic appeal.
4. Industrial Machinery
Many industrial machinery parts, such as gears and brackets, benefit from the precision and strength offered by pressure die casting, enhancing performance and longevity.
Key Materials Used in Pressure Die Casting
The choice of material is crucial in determining the performance of pressure die casting products. Common materials include:
- Aluminum Alloys: Widely used for their lightweight and excellent corrosion resistance.
- Zinc Alloys: Known for their durability and ease of casting into complex shapes.
- Magnesium Alloys: Utilized in applications where weight reduction is crucial.
The Future of Pressure Die Casting
As technology advances, the future of pressure die casting looks promising. Innovations such as:
- Advanced Simulation Software: This allows for better mold design and process optimization.
- Automation and Robotics: The integration of automated systems enhances precision and reduces production times.
- Environmentally Sustainable Practices: Efforts to use eco-friendly materials and recycling methods are on the rise, aiming to minimize the impact of manufacturing on the environment.
The Role of Quality Control in Pressure Die Casting
Ensuring that pressure die casting products meet industry standards involves rigorous quality control measures. This includes:
- Dimensional Inspection: Uses tools such as calipers and gauges to check the accuracy of produced parts.
- Non-Destructive Testing: Techniques like ultrasonic testing and X-ray inspections help identify internal defects.
- Surface Finish Evaluation: Assessing the surface quality to conform to design specifications.
Choosing a Reliable Manufacturer for Pressure Die Casting Products
When selecting a manufacturer for your pressure die casting products, it's essential to consider:
- Experience: Look for a company with a proven track record in pressure die casting.
- Quality Certifications: Ensure the manufacturer adheres to recognized quality standards.
- Customer Support: A responsive support team can make a significant difference in your overall experience.
- Technology and Equipment: A manufacturer equipped with the latest technology will likely produce higher quality products.
Conclusion
In conclusion, pressure die casting products represent a vital component of modern manufacturing, delivering high-quality, cost-effective solutions for a variety of industries. Understanding the nuances of this technology, along with its benefits and applications, is essential for businesses looking to harness its potential. As we advance, the future of pressure die casting will undoubtedly continue to evolve, offering even more innovative solutions to meet the demands of the market.
For companies seeking reliable and high-quality metal fabricated products, visit deepmould.net to explore our offerings in pressure die casting and other metal fabrication solutions.