The Vital Role of Injection Mold Tool in Metal Fabrication
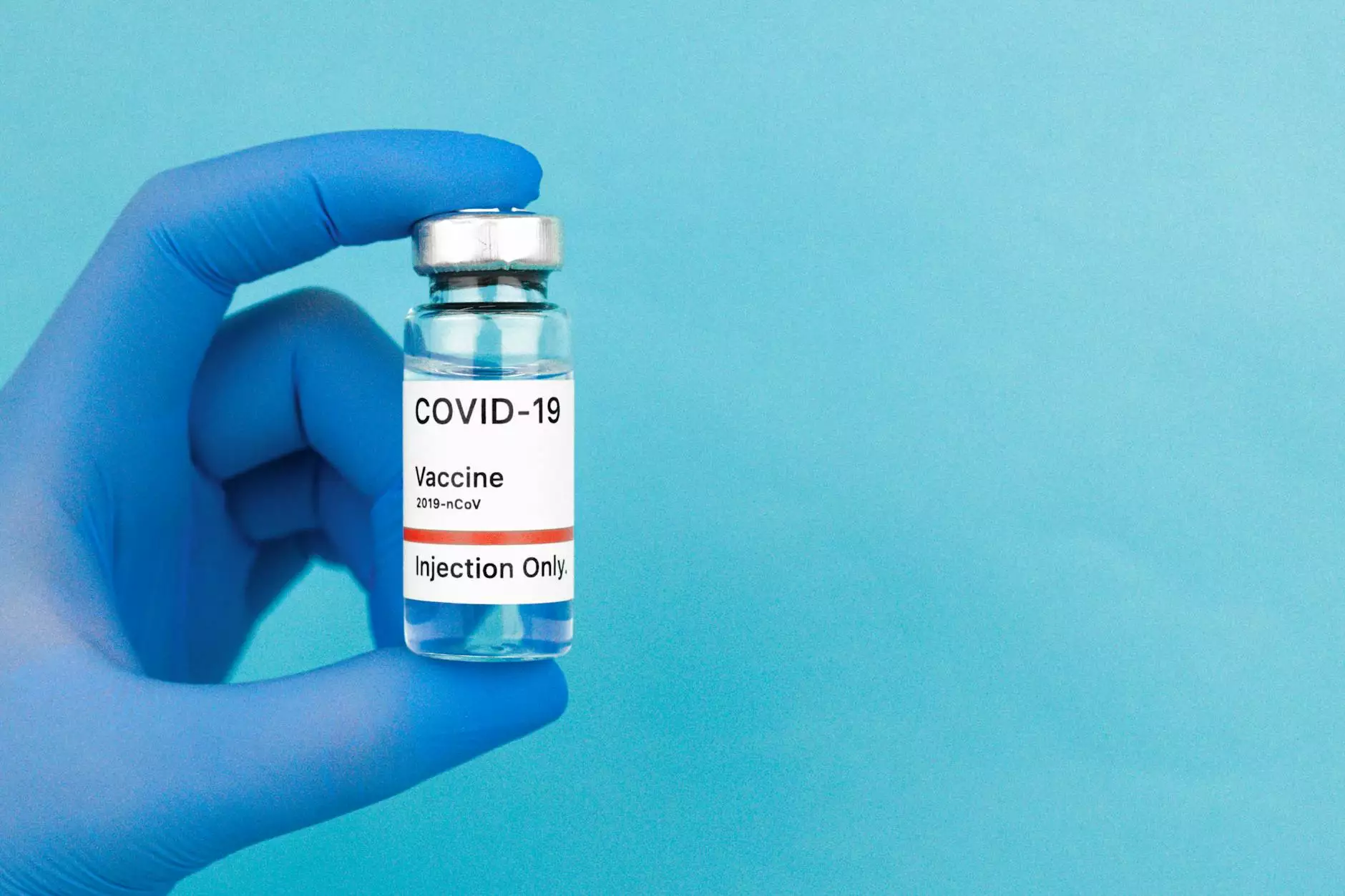
Injection mold tools are pivotal in the manufacturing industry, especially for metal fabricators looking to create precise and durable components. This article delves deep into what injection mold tools are, their applications, and why they are essential for businesses striving for efficiency and quality in production.
What is an Injection Mold Tool?
At its core, an injection mold tool is a device employed in the injection molding process, used to shape molten material into a specific form. This tool typically consists of two main components: the mold itself and the injection mechanism. The mold contains a cavity that outlines the desired shape of the finished product, while the injection system forces the material into the mold under high pressure.
The Process Behind Injection Molding
The injection molding process uses an injection mold tool in several stages to produce high-quality parts efficiently:
- Material Preparation: The raw material, often plastic or metal, is first heated until it melts.
- Injection: The molten material is injected into the mold cavity, where it fills the entire space.
- Cooling: The material cools and solidifies, taking on the exact shape of the mold.
- De-Molding: Once hardened, the mold opens, and the finished product is removed.
This process allows for quick, repeatable, and high-precision production runs, making it a favored choice among metal fabricators.
Advantages of Using Injection Mold Tools
Utilizing an injection mold tool presents several advantages for businesses in the manufacturing sector:
- High Precision: Injection molding guarantees a high level of accuracy and consistency in product details.
- Cost-Effectiveness: After the initial investment in molds, injection molding is highly efficient, reducing per-unit costs for large production runs.
- Material Versatility: Various materials can be used, including different types of plastics and metals, offering flexibility depending on project themes.
- Reduced Waste: The precise nature of injection molding results in less scrap material compared to other manufacturing methods.
- Complex Designs: Injection mold tools can create intricate shapes and complex geometries that may be challenging with other techniques.
Applications of Injection Mold Tools in Metal Fabrication
The versatility of injection mold tools makes them indispensable in numerous applications, spanning various industries:
1. Automotive Industry
In the automotive sector, injection molding is essential for producing components such as dashboards, bumpers, and housing for critical electrical systems. The precision of the injection mold tool ensures safety and efficiency in the final products.
2. Consumer Electronics
With the rapid advancement of consumer electronics, manufacturers rely on injection molds to produce sophisticated devices and components, including mobile phone casings and other intricate parts.
3. Medical Devices
In the medical field, where precision is tantamount, injection mold tools aid in creating critical equipment like syringes, surgical instruments, and various types of implants.
4. Packaging
Injection molding is commonly used for creating packaging solutions that require high durability and resistance to various environmental factors, such as moisture and temperature.
Choosing the Right Injection Mold Tool
Selecting the appropriate injection mold tool is crucial for ensuring the success of any manufacturing endeavor. Here are key considerations:
- Material Compatibility: Ensure the tool is compatible with the type of material being used.
- Mold Design: Evaluate the complexity of the design to confirm that the mold can deliver the required specifications.
- Production Volume: Consider how many units you plan to produce—the tool should be effective for your production scale.
- Budget: Balance the cost of tooling with the machine operation to ensure profitability.
The Future of Injection Mold Tool in Manufacturing
The landscape of manufacturing is evolving, and so is the role of injection mold tools. Innovations in technology—the integration of automation and smart manufacturing—are paving the way for more efficient production processes. Here are some trends to watch:
1. Automation and Robotics
The integration of robotic systems in the injection molding process enhances efficiency, reduces human error, and increases safety in the workplace. Automated systems can handle the entire process from injection to de-molding.
2. Advanced Materials
Research into new materials that can withstand extreme conditions continues to influence injection molding. Innovations in composites and alloys are opening new frontiers for injection mold tools in metal fabrication.
3. Sustainable Practices
With growing environmental concerns, manufacturers are seeking biodegradable materials and sustainable practices in the injection molding process. Tools that reduce energy consumption and waste will become increasingly valuable.
Conclusion
In summary, the significance of the injection mold tool in the field of metal fabrication cannot be overstated. By providing manufacturers with the ability to produce high-quality, precise components efficiently and cost-effectively, injection molding remains a cornerstone of modern manufacturing. With ongoing advancements and a growing emphasis on sustainability, the future of injection mold tools looks promising, making it an essential consideration for any metal fabricator looking to enhance their operations.
About DeepMould.net
DeepMould.net specializes in providing high-quality injection mold tools for various industries, ensuring that we meet the demands of modern production while maintaining the highest standards of service. Our expertise in metal fabrication allows us to customize and optimize tools for any project, ensuring both efficiency and excellence.