The Power of Plastic Injection Molding in Modern Manufacturing
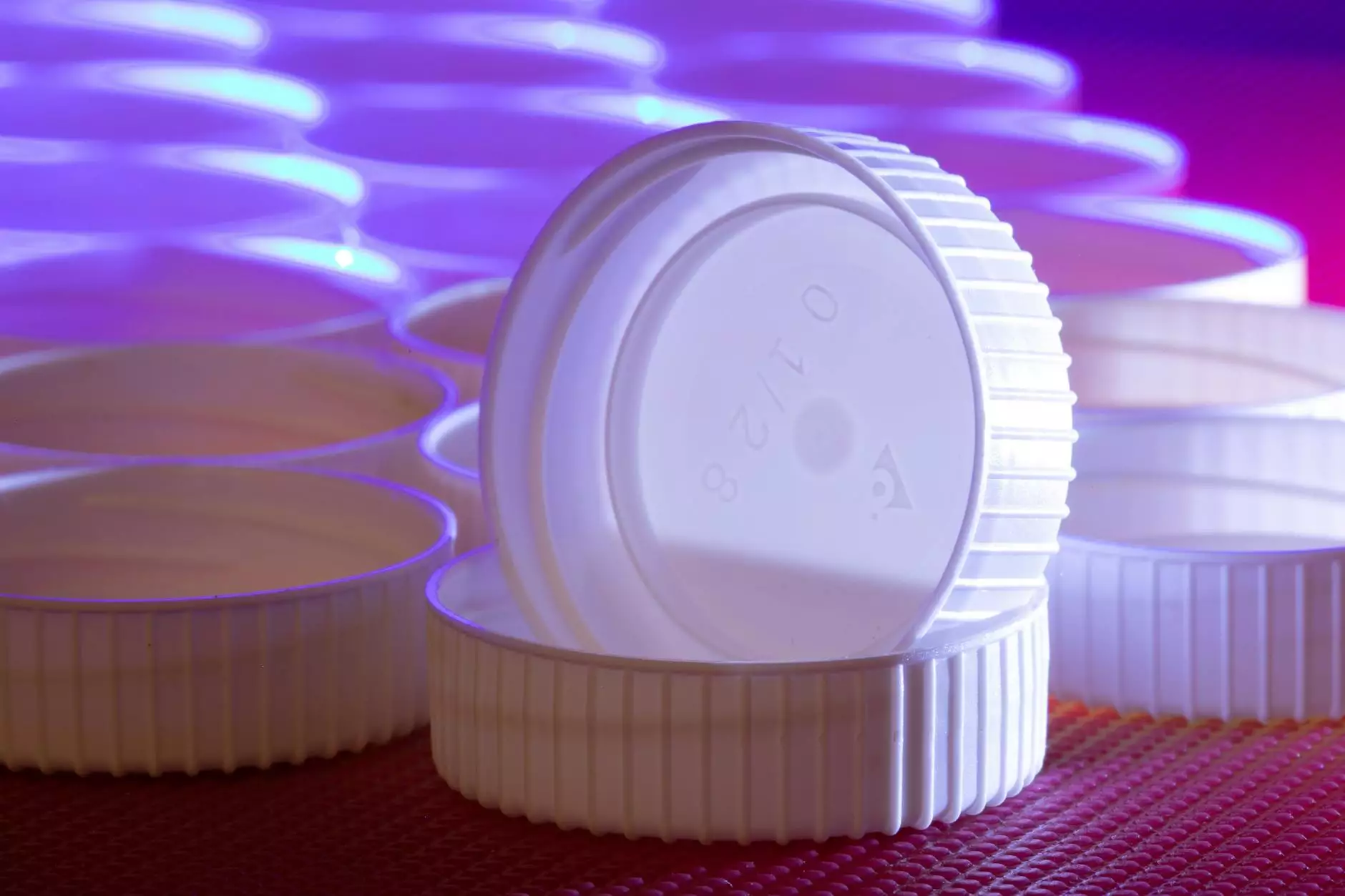
Plastic injection molding has redefined the landscape of manufacturing by providing a versatile, efficient, and cost-effective method for producing a wide variety of plastic components. This technique is not only pivotal for the creation of plastic products but also plays an invaluable role in the metal fabrication sector. In this comprehensive article, we will delve into the intricacies of plastic injection molding, its applications, advantages, and its significant impact on various industries.
Understanding Plastic Injection Molding
At its core, plastic injection molding is a manufacturing process that involves injecting molten plastic into a mold to create specific shapes and designs. The process begins with the selection of the appropriate plastic material, which is then heated and injected into a mold under high pressure. Once the plastic cools and hardens, the mold is opened, and the finished part is ejected. This method allows for the production of complex and intricate parts with high precision and repeatability.
Key Components of Plastic Injection Molding
The plastic injection molding process involves several essential components that work together to ensure efficient production:
- Injection Molding Machine: The heart of the process, responsible for melting and injecting the plastic.
- Mold: The custom-made cavity where the molten plastic is injected to form the desired shape.
- Material Hopper: A storage container that holds the raw plastic pellets until they are required for injection.
- Heating Elements: These elements melt the plastic in the barrel of the injection machine.
- Cooling System: Helps in cooling the mold to solidify the injected plastic quickly.
The Process of Plastic Injection Molding
The plastic injection molding process typically involves the following steps:
- Material Selection: Choosing the appropriate plastic material based on the desired properties of the final product.
- Melting: The selected plastic is fed into a heated barrel where it is melted until it reaches a specific viscosity.
- Injection: The molten plastic is injected into the mold at high pressure, filling all the cavities.
- Cooling: The injected plastic is cooled within the mold, allowing it to solidify into the desired shape.
- Ejection: Once cooled, the mold is opened, and the finished product is ejected.
Applications of Plastic Injection Molding
Plastic injection molding is widely utilized across various industries due to its flexibility and efficiency. Some of the primary applications include:
- Consumer Products: From toys to household items, plastic injection molding is used to produce countless everyday products.
- Automotive Parts: This process is essential for creating durable and lightweight components in the automotive industry, including dashboards, exterior panels, and clips.
- Medical Devices: Precision is crucial in the manufacture of medical devices and components, making injection molding a preferred choice.
- Electronics: Many electronic housings and components are produced using this technique, ensuring reliability and performance.
- Packaging: The packaging industry benefits from injection molding to produce safe, durable, and user-friendly containers.
Advantages of Plastic Injection Molding
The popularity of plastic injection molding can be attributed to its numerous advantages, including:
- High Efficiency: Once the mold is created, the production of parts is rapid and can yield thousands of units per hour.
- Cost-Effectiveness: Although tooling can be expensive, the low cost per unit at high volumes offsets this investment.
- Precision and Consistency: Injection molding allows for high precision, resulting in uniform products that match specifications closely.
- Material Variety: A broad range of thermoplastics and thermosetting polymers can be used, providing flexibility in material selection.
- Minimal Waste: The process generates very little waste, as excess material can usually be reprocessed for future use.
Challenges in Plastic Injection Molding
While plastic injection molding offers many benefits, it is not without its challenges:
- High Initial Costs: The cost of designing and manufacturing molds can be substantial, impacting the overall project budget.
- Mold Design Complexity: Designing effective molds that account for material shrinkage and flow can be a complex task.
- Material Limitations: Some plastics may not be suitable for certain applications due to temperature or structural constraints.
Plastic Injection Molding in Metal Fabrication
The relationship between plastic injection molding and metal fabrication is growing stronger. In many cases, businesses in the metal fabrication sector are integrating plastic injection molding to enhance their product offerings. Here’s how:
Hybrid Components
Many modern products require both metal and plastic components. By incorporating injection molded parts with metal, manufacturers can create hybrid components that leverage the strengths of both materials. This integration can lead to lighter, more efficient parts that offer enhanced performance.
Tooling and Fixtures
In metal fabrication, specialized tooling and fixtures are often required to work with metal parts. Producing these tools using plastic injection molding can reduce costs and manufacturing time.
Prototyping
Plastic injection molding can be used for rapid prototyping of metal parts, allowing for testing and validation before full-scale metal production, thus saving time and resources.
The Future of Plastic Injection Molding
The future of plastic injection molding is poised for exciting advancements, particularly with the increasing adoption of automation and advanced technologies:
Automation and Robotics
The integration of robotics into the injection molding process is shaping the future of manufacturing. Automated systems can enhance efficiency and precision while reducing labor costs.
Smart Manufacturing
Implementing Industry 4.0 practices, including the Internet of Things (IoT), will enable manufacturers to monitor and optimize the injection molding process in real-time, improving overall productivity.
Sustainable Practices
As environmental concerns grow, there is a push towards sustainability in manufacturing. The use of recycled materials in plastic injection molding is gaining popularity, along with innovations in biodegradable plastics.
Conclusion
In conclusion, plastic injection molding is a transformative technology that has become indispensable in modern manufacturing. Its applications span numerous industries, and its benefits of efficiency, precision, and cost-effectiveness are unmatched. As advancements in technology continue to emerge, plastic injection molding will likely evolve further, integrating more sophisticated processes that enhance productivity and sustainability. For businesses in the metal fabrication sector, embracing this technology could mean a step towards greater innovation and competitiveness in the marketplace.
For more information on how plastic injection molding can benefit your production processes, visit DeepMould.net today.